We Build Cool Stuff
Learn about the Big Boy 3D Printer and the people behind it
About us
The Big Boy 3D Printer
An Incredibly Overbuilt 3D Printer that has elements of generative design, a custom tool changer, and lots of rigidity.
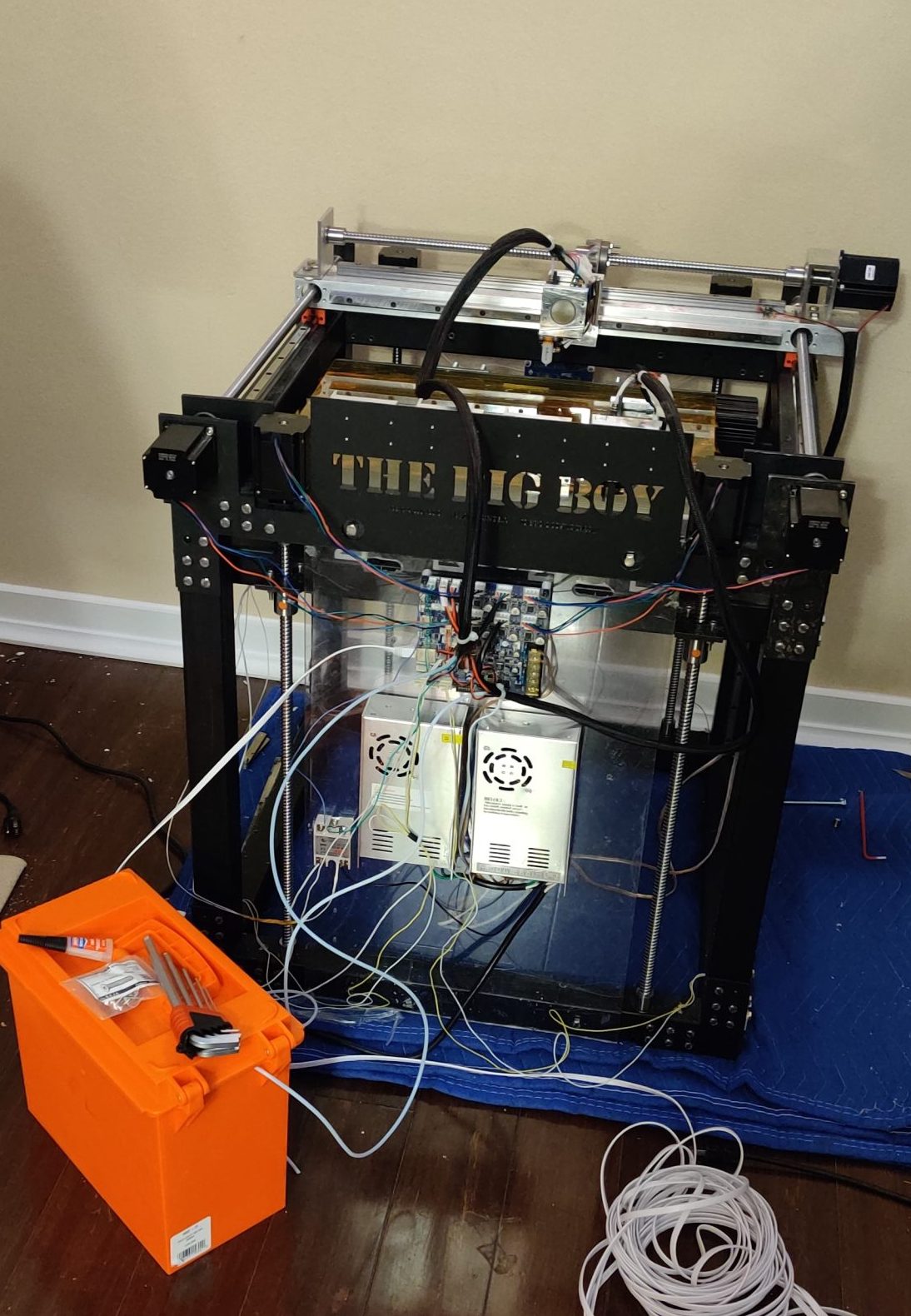
Project Goal
Learn additive and subtractive Manufacturing methodology and The Design Process by building an experimental 3d printer/mill hybrid from scratch.
Print Area of 330mm x 475mm x 500mm
We tried to design with the biggest print area we could reasonably manufacture.
Overall Size: 700mm x 700mm x 900mm
Our requirement was for the printer to fit through a standard door. We were able to meet that requirement.
Weight: Approximately 250 lbs
Since this is steel construction through and through, the printer weighs a fair bit. This weight and rigidity make it easy to add a spindle.
Project Updates
Designing With Future Use Cases in Mind
The advent of 3D printing has revolutionized the way we...
Read More
Alan Kraft
- Purdue Nuclear Engineering Alum
- Chief Engineer on the Project
- Master of CAD
- Procured Ball Screws and Rails
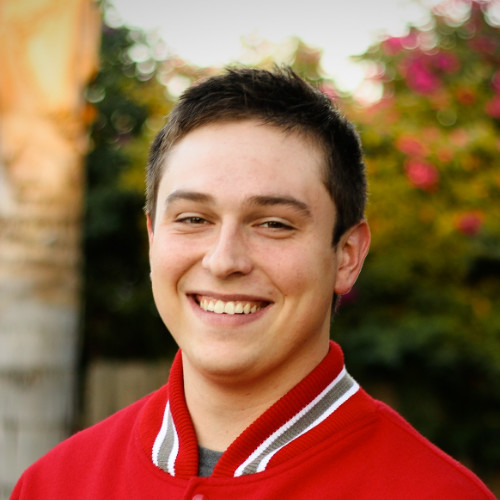
Alex Josten
- Purdue Aeronautical Engineer
- Master of CAM
- Main Manufacturer
- Made all Tubes and Couplers
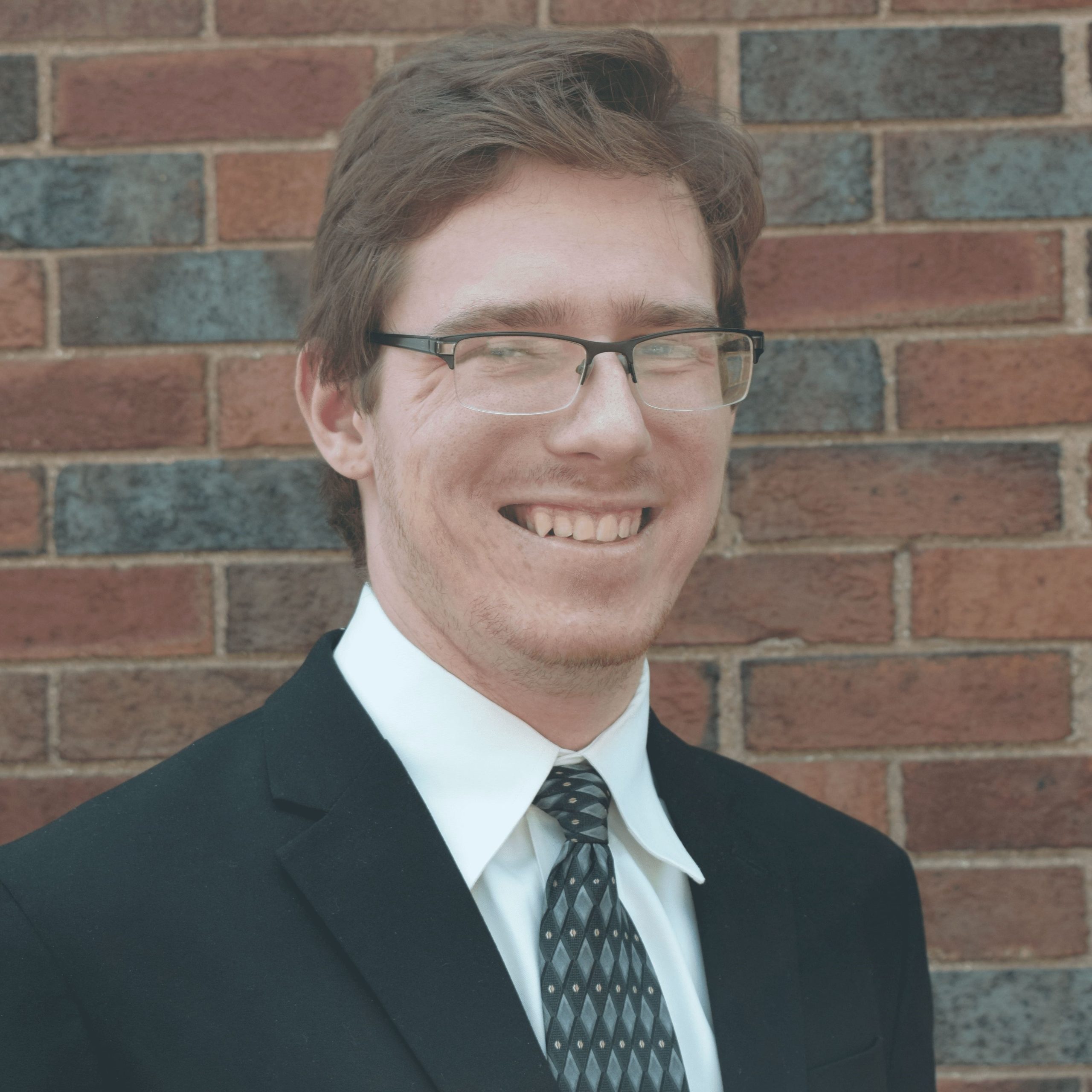
Matthew Fitzgerald
- Purdue Systems Analysis and Design Alum
- Worked on Procurement
- Designed Electronics
- Manufactured Gusset Plates